WHEN PLASTIC WAS first introduced in 1907, it was hailed as a miracle material. The petroleum-based substance could seemingly do anything — harden into a rock-solid car part or a flexible waterproof coating, stretch into fibers, froth into foam, and take on any shade (from the deepest black to stark white to translucent).
But over a century years later, it’s impossible to ignore the fact that plastic is no longer a miracle, and rather a massive problem.
Per capita, we all go through over 300 pounds of plastic annually. Most of it ends up in landfills or floating ocean garbage patches, which now contain over 5 trillion pieces of plastic.
These materials break down excruciatingly slowly; scientists estimate that it will take nearly half a century for a single-use plastic water bottle to fully disappear into a landfill. And even then, its byproducts — namely, microplastics, carbon dioxide, and so-called “forever chemicals” — aren’t exactly environmentally friendly.
But what about plastics that are designed to degrade safely? New foam materials could disappear in seawater and prevent even more litter from invading the world’s oceans, according to a recent study published in the journal Science of the Total Environment.
HERE’S THE BACKGROUND — To solve our substantial plastic waste problem, researchers have offered three main solutions, each with their own pros and cons: recycling, bio-based plastics, and plastics that biodegrade.
It’s worth unpacking the differences between each of these terms, as people often get them confused. Recycling is simply repurposing old plastic into a new product; it doesn’t get rid of the material, but it can cut back on the amount of new plastics entering the market.
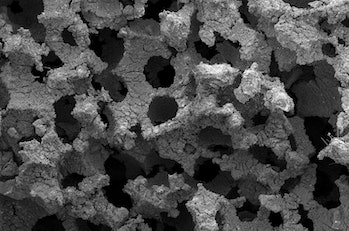
Bio-based plastics (often shortened to bioplastics) are a group of materials made from sources other than fossil fuels, like plants or fungi. Some are recyclable, and some are biodegradable. But not all of them: Think of amber resin, which is made completely from plants, but famously lasts millions of years. After all, it made the Jurassic Park plot somewhat plausible.
Finally, there’s biodegradable plastic. All plastics break down given enough time (up to 1,000 years), but what sets biodegradable plastics apart is that they can be eaten and digested by microorganisms to speed things up. And a new discovery could make this process a bit easier.
WHAT’S NEW — The recent study promises to bring us closer to unlocking fully biodegradable plastic products that disintegrate in any environment, including the ocean. Using their new technique, scientists plan to craft shelf-ready goods, such as sneakers, by essentially cutting out the middleman (crude oil).
“Plastics come from petroleum. Petroleum comes from algae,” says Stephen Mayfield, a biochemist at the University of California San Diego and co-author of the new study. So, he and his team thought, “Let’s make plastics directly from algae.”
The result was a bio-based polyurethane plastic that can be completely broken down by microbes in just a few months. Mayfield’s team has fashioned this new material into surfboards, shoes, foams, and even waterproof coatings. Now, they’ve concocted a version that biodegrades in seawater.
WHAT THEY DID — Coaxing plastic to break down in the ocean is trickier than you might expect.
“Foam is an incomplete food,” Mayfield says. In order for any material to be fully biodegradable, it must provide a complete meal to the microorganisms looking to eat it. After all, you wouldn’t be satisfied with merely a block of salt or a dash of paprika.
This isn’t an issue on land, since soil is packed with micronutrients like nitrogen, magnesium, and countless other trace elements that microbes use to meet their needs. But in the sea, such micronutrients are much harder to come by.
To get their polyurethane to biodegrade in such an environment, Mayfield’s team enriched their algae-based plastic with substances such as succinic acid (somewhat like how companies add vitamins to breakfast cereal).
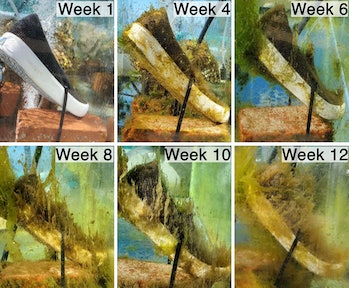
They tested it out by submerging chunks of foam and shoes both in a tank filled with seawater and in various spots in the Pacific Ocean. Over test periods ranging from three weeks to several months, they found that the samples had changed color and were covered in creatures like crabs, seaweed, and itty-bitty crustaceans — and unlike a control material, the polyurethane showed visible signs of crumbling.
To take a closer look at some of the foam samples, the team used scanning electron microscopy, which captures images with a beam of electrons, and were able to peek at the granular signs of decay.
The finished product will soon be available through Algenesis, a spinoff company that Mayfield helped found.
HERE’S THE CATCH — Conceiving a new product is one thing; convincing people to buy it is another. And biodegradable plastics are a hard sell. Part of this comes down to cost: “Green” plastics, especially single-use ones, tend to be pricier compared to traditionally formulated plastics.
But there’s also consumer distrust — many people in the target market are simply disillusioned by constant corporate greenwashing, Mayfield says, and may not believe that products marketed as “recycled” or “biodegradable” actually are.
“Very few biodegradable plastics actually make it as products, just like very few good-looking actors are Brad Pitt,” says Gadi Rothenberg, a sustainable chemist at the University of Amsterdam in the Netherlands who was not involved in the study.
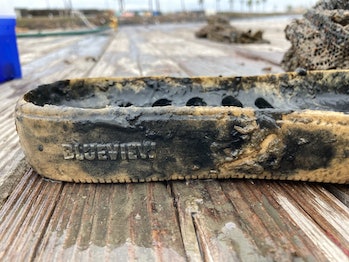
Rothenberg’s own company, Plantics B.V., started out making a biodegradable plastic product, and now produces recyclable and bio-based plastics.
Ultimately, though, Rothenberg feels that biodegradable plastics aren’t a good alternative to cutting back on plastic use altogether. All plastics are made of carbon, he points out, which can wind up back in the atmosphere as planet-heating carbon dioxide once it’s no longer stored away as a shoe or a soup spoon.
Even completely biodegradable plastics can emit carbon dioxide. And many plastics, including polyurethane, release additional chemical compounds, like hydrogen cyanide and nitrogen oxides, if they’re burned.
“The fact that it may or may not break down once it gets into the ocean is not important, because you should not have it in the first place,” Rothenberg explains. In his view, the best course of action is to reduce our dependence on plastics of any kind.
WHAT’S NEXT — Future plastics come with plenty of possibilities. Companies like Algenesis and Plantics B.V. will continue to look into new ways of creating fully recyclable, bio-based, and/or biodegradable products.
In the meantime, initiatives like The Ocean Cleanup are developing technology to recycle the billions of tons of conventional plastic that we already have. The organization claims it can tidy up the entire Great Pacific Garbage Patch, which contains up to 1.8 trillion pieces of trash, with giant nets. But not everyone is convinced this ambitious plan will work.
Ultimately, Rothenberg and Mayfield agree the success of such initiatives will likely depend on economics. “It’s either you find [a material] that’s cheap, or the market price of oil really has to go up,” Rothenberg says.